The Modern Manufacturing Blueprint for Aerospace and Defense
.avif)
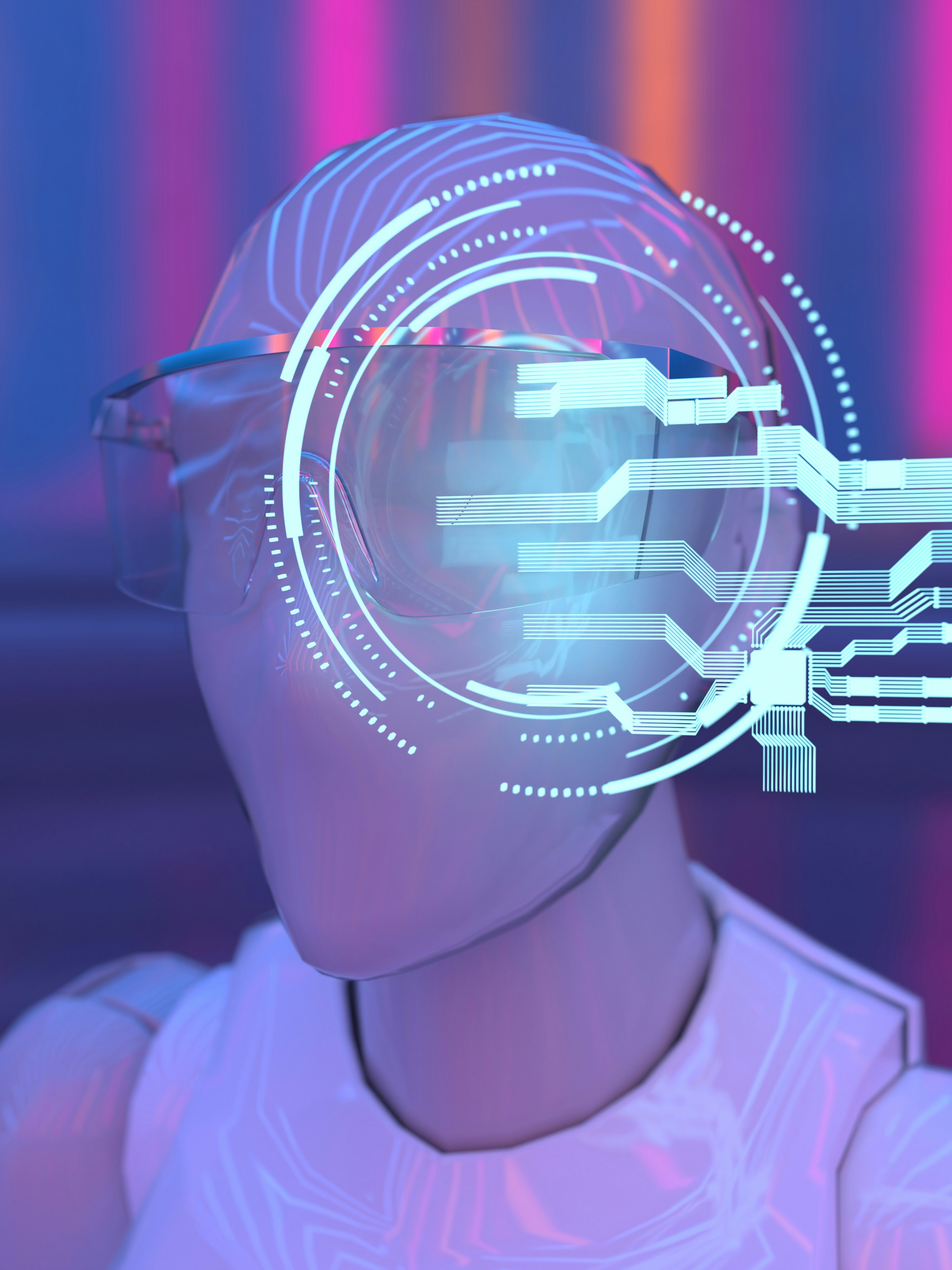
Aerospace and defense manufacturing is a multi-step, highly specialized process that transforms raw materials into flight-ready systems. It begins with the sourcing and preparation of foundational materials. These include rare earth elements, which are essential for sensors, electronics, and high-performance permanent magnets. They also include specialty alloys or composite resins, which form the structural backbone of airframes, missiles, UAVs, and satellites. These materials are transformed through processes like composite fabrication, producing lightweight yet rigid component parts ideal for aerodynamic and heat sensitive application. Forging is also used to enhance the strength and durability of metal parts.
Once shaped, these components go through a precision manufacturing stage, where CNC machining equipment is used to cut, shape, and finish metal or composite parts to exact tolerances. The smallest deviation in a part’s dimensions can compromise safety and performance, so in order to meet the rigorous demands on speed, pressure and temperature, these parts are often required to meet specifications with 0.001 of an inch or less.
Afterward, finished parts undergo a rigorous inspection and QA process in conjunction with certification and compliance requirements. Throughout, the supply chain is governed by strict standards like AS9100, ITAR, and NADCAP, ensuring that each part meets not just mechanical specifications, but also national security requirements. Once these sub component parts pass certification, they move into sub-assembly, where they are integrated into larger structures like airframes, missiles, or satellite systems.
A Manufacturing Base Under Strain
The U.S. aerospace and defense manufacturing base faces critical challenges across nearly every layer of production. There are shortages of domestic rare earth processing, and limited capacity for forging houses, composites fabricators, and precision manufacturing shops. Most machining, composites, and finishing work is done by fragmented, under-digitized vendors that lack aerospace and defense compliance certification. There's also a shortage of cleared, agile sub-assembly and integration facilities, especially for emerging programs in hypersonics, space, and UAVs. These issues collectively result in long lead times, brittle supply chains, and growing backlogs for critical defense programs.
Lead times across aerospace and defense manufacturing are often long and unpredictable, with forging taking 6–18+ months, composite fabrication 12–16+ weeks, and precision machining 8–12+ weeks. These delays are compounded by the industry's highly fragmented supply chain, where each manufacturing stage—material sourcing, composites, forging, machining, post-processing, and assembly—is handled by different, siloed vendors, many of whom lack digital infrastructure or certification readiness. In addition, the industry faces a growing skilled labor shortage, with many experienced machinists, fabricators, and inspectors retiring and too few younger workers entering the field.
Because these suppliers operate independently, there’s often little coordination, no shared traceability, and inconsistent quality standards. It’s common for a single flight-critical part to pass through 5–10 separate shops, each introducing risk for delay, rework, or compliance failure. This fragmented model drives up cost, slows innovation, and creates a brittle manufacturing base.
Reshaping Aerospace and Defense Production
Composites Manufacturing
Composites are essential in defense and flight systems due to their high strength-to-weight ratio and thermal resilience. While a few major fabricators handle large airframe and space vehicle production, the aerospace and defense sector is in dire need of agile and secure small-batch composite vendors. This is especially true for the growing demand for hypersonics, satellite systems, and advanced UAVs.
Traditional composite fabrication—particularly autoclave curing—is costly, slow, and constrained by limited capacity. To address these gaps, manufacturers are shifting toward Out-of-Autoclave curing methods, enabling lower-cost, scalable production without compromising structural performance. Alongside this, automated composite layup technologies and predictive resin curing models are being adopted to optimize cycle times and improve consistency across both large-scale and low-volume, complex parts.
By embedding sensors and machine vision into the fabrication process, manufacturers can perform real-time quality inspection and detect anomalies at the point of production, reducing waste, increasing yield, and accelerating the path to certification. These innovations are especially critical for producing composites for UAVs, missiles, and space systems, where weight, thermal resistance, and structural integrity must be precisely balanced.
Forging
Many U.S. forging facilities are decades old, using legacy presses, hammers, and hydraulic systems that date back to the Cold War. Forging remains a cornerstone of aerospace manufacturing, yet the U.S. forging base suffers from chronic underinvestment and extended lead times, particularly for exotic alloys used in aerospace and defense applications.
Large forging presses can cost $50M–$150M+, so only a few large players dominate large-scale aerospace and defense grade builds. Small batch, highly complex component parts are underserved by these legacy suppliers however, so a fragmented network of underdigitized forging houses struggles to provide capacity for critical new defense programs in hypersonics, satellite systems, and advanced UAVs.
An emerging class of supplier is filling this void, developing processes optimized for cutting edge small batch critical components. They are integrating AI prediction and optimization modeling into their processes and leveraging near-net shape forging techniques to minimize material waste and machining time. Advanced simulation tools now allow engineers to model forging outcomes for advanced alloys based on real-time parameters like temperature, pressure, and cooling rate, reducing trial-and-error and enabling faster tool development.
Machining
The U.S. machining industry is made up of over 25,000 machine shops, the majority of which are small, family-run businesses with limited digital infrastructure. Many of these shops struggle to meet modern compliance standards like AS9100, ITAR, and NADCAP, and lack the capacity or technical capability to handle small-batch, high-complexity parts.. As a result, they are poorly equipped to serve the fast-evolving needs of defense programs. Compounding the problem is a severe skilled labor shortage, with an aging workforce retiring at a rapid pace and too few younger machinists entering the field.
There is a growing opportunity in building fully compliant autonomous precision manufacturing facilities, capable of working with exotic materials needed for rapid prototyping and low-rate production for mission-critical programs. As legacy suppliers struggle to meet the speed, complexity, and compliance requirements, end to end facilities that offer advanced manufacturing, inspection, and certification offer a compelling alternative.
Quality, Compliance & Traceability
In a sector with strict performance and safety requirements, quality control and compliance are demanding, but the current systems are manual and often siloed. Legacy QA systems are designed to inspect the finished product, but offer little insight into in-process quality risks. The opportunity now is to impliment real-time defect detection and predictive quality modeling across the entire supply chain, from material input to final inspection.
Efforts are also accelerating to create a secure, digital ledger of QA and compliance data capable of integrating with a range of supplier systems and capturing inspection reports, material certs, and process logs in one traceable, auditable platform. This is vital for navigating ongoing AS9100 and NADCAP certifications, particularly for small shops that often lack dedicated compliance resources. Automating inspection workflows, digitizing first article documentation, and sharing quality data securely across tiers can dramatically reduce rework, cycle time, and compliance risk.
Additive Manufacturing
Traditional aerospace manufacturing methods like forging, casting, and machining excel in large structural components (fuselages, wings) and high-stress, high-temperature parts. They are also cost-effective for simple, high-volume production. However, these methods struggle with complex, low-volume components and rapid prototyping. Additive manufacturing addresses these limitations and is increasingly used for parts like rocket engine nozzles, satellite brackets, and lightweight UAV structures. Unlike traditional tooling, which can be slow and costly, additive manufacturing enables rapid prototyping of unique flight-test components, effectively filling a critical gap in the existing aerospace and defense manufacturing system, and fills a void where the existing aerospace and defense manufacturing system struggles.
While additive manufacturing is well-established for rapid prototyping and non-critical, low-volume parts that don’t require certification, its significant growth potential lies in complex and flight-certified components. Achieving this requires automated post-print inspection, certification workflows, and compliance-ready documentation Furthermore, leveraging AI modeling to simulate crucial performance indicators like heat distribution and structural integrity during printing is essential to meet the very specific requirements for these high complex components. Another significant opportunity for additive manufacturing is part consolidation, where multiple traditionally joined components are produced as a single, integrated structure, leading to reduced complexity, weight, and potential failure points.
—
Aerospace and defense manufacturing is approaching an inflection point. As legacy infrastructure strains under rising demand and emerging geopolitical threats, the path forward requires rethinking every layer of production—from material sourcing to final assembly. The opportunity lies in building a next-generation manufacturing base: one powered by automation, digital traceability, real-time quality control, secure digital compliance, and AI-powered optimization across the full production lifecycle.
James Murphy is Forum’s Managing Partner, leading the Investment team in finding bold, ambitious SaaS founders. Connect with him on Linkedin and X.
Latest Thought Pieces
.avif)