Mining the Future: The Rare Earth Crisis Shaping U.S. Industrial Power
.avif)
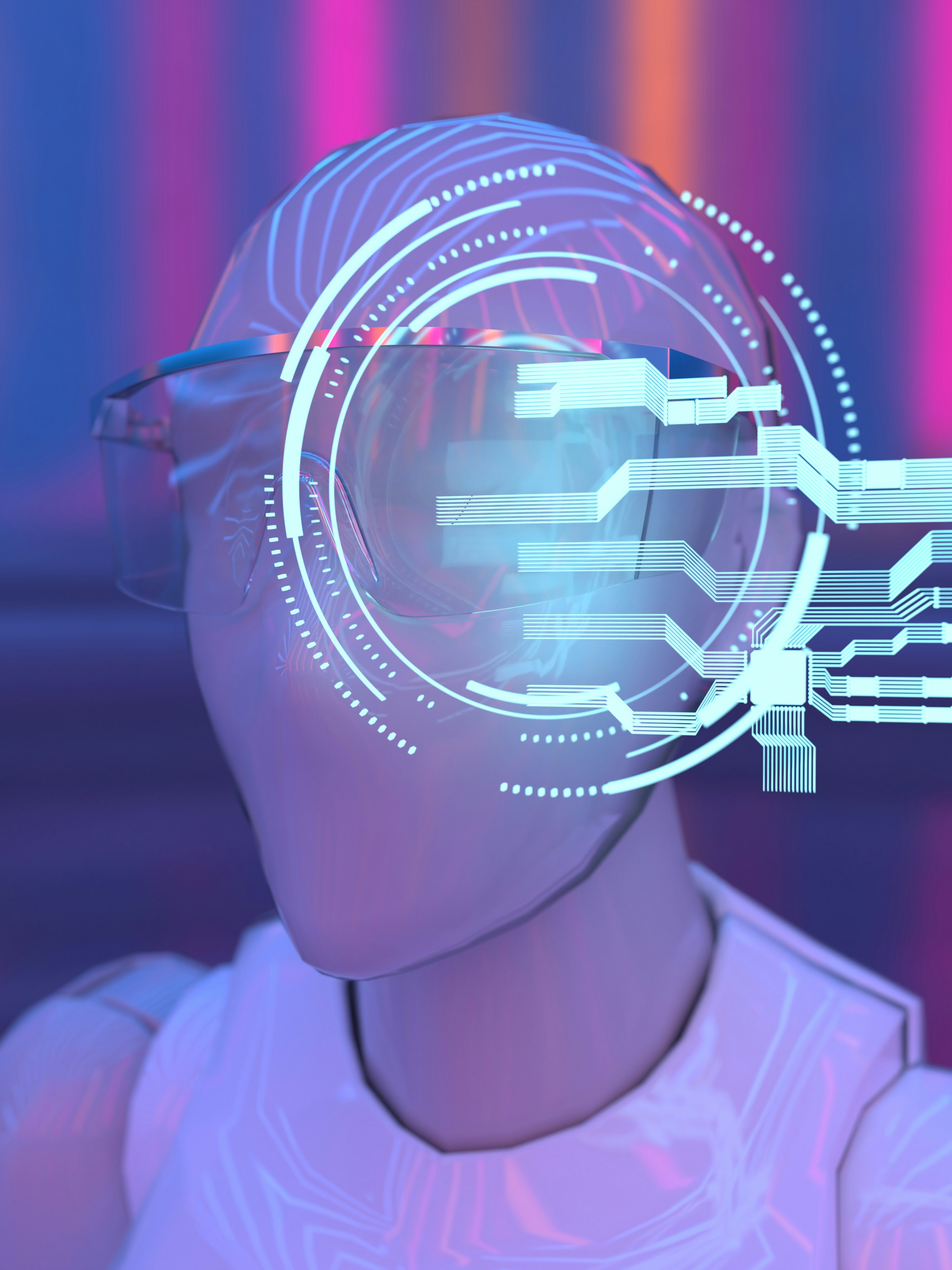
This is the first in a series of articles breaking down this emerging crisis, the United States efforts to build a stable and diversified rare earth element supply chain, and the implications across the Aerospace, Robotics and Defense sectors.
Rare earth elements (REEs) are a group of 17 metallic elements that are essential in modern technology due to their unique magnetic, conductive, and luminescent properties. They are crucial in the manufacturing of critical input components across aerospace, defense, robotics, and AI Hardware. Some examples include:
- High density batteries
- Permanent magnets
- Optical sensors
- Actuators
- High strength alloys and composites
- Precision bearings
- AI semiconductor materials
- High-energy capacitors and supercapacitors
- High-frequency RF and secure communications components
Given their importance across critical infrastructure and national security, ensuring a stable and diversified supply chain is a top priority for the U.S. and our allies. To date the U.S. has been almost exclusively reliant on China for these critical elements, but over the next decade, control of the REEs supply will have massive geopolitical implications.
Rare Earth Mining and Refining
Rare earth minerals are actually quite common in the Earth's crust, but they are rarely found in high enough concentrations to be easily mined. Despite their name, rare earth elements are about as abundant as metals like copper or nickel, but they are typically spread out and mixed with other minerals rather than appearing in large, concentrated deposits.
The challenge isn't finding them—it’s extracting and refining them efficiently. They are primarily extracted through open-pit mining, where large-scale excavation exposes ore deposits within the Earth’s crust. Once mined, the ore undergoes a multi-step refinement process, first being crushed into a fine powder before being treated with powerful acids and chemical solvents to separate the rare earths from surrounding minerals. However, this process generates significant environmental challenges, producing toxic waste and radioactive byproducts such as thorium and uranium, which, if not properly managed, can contaminate soil, air, and water sources
The Emergence of China
Throughout the 1980s and 1990s, the United States played a dominant role in both the extraction and refining of rare earth elements. At the center of this industry was the Mountain Pass Mine in California, which stood as the world’s leading supplier. During this period, the U.S. was responsible for roughly 33% of global REE production, and nearly all of the rare earths extracted at Mountain Pass were processed and refined domestically, ensuring a stable and self-sufficient supply chain.
Beginning in the late 1980s, China identified rare earth elements as a critical resource and strategically expanded both mining and refining operations. Over the following decade, the Chinese government heavily subsidized REE production, and established a state-backed, vertically integrated industry designed to dominate the global supply chain. This strategic shift was part of a broader push to develop manufacturing capabilities in critical sectors, particularly in electronics and advanced technologies. During this same period, the United States was moving in the opposite direction. U.S. policymakers and corporations prioritized deindustrialization and outsourcing, shifting focus toward higher corporate profits and sectors such as financial services, software, and high-tech industries. By the late 1990s, China had not only outcompeted the U.S. in manufacturing but had also cemented its dominance in REE production, securing control over a resource essential to modern technology and national security.
China’s Monopoly
Today China has emerged as the unencumbered leading exporter of REEs. They control over 70% of extraction, and 85% of the world’s refining - including near monopolies in a select group of some of the most critical elements. To date, no other nation has developed the infrastructure to mine and refine REEs at scale.
This is driven by three main factors: low labor costs, lax environmental regulations, and heavy government subsidies. The Chinese government has invested billions into REE infrastructure, allowing state-backed companies to undercut global competitors and control capacity. Additionally, China’s loose environmental policies allow for highly polluting extraction methods, which many Western nations like the United States have banned.
Weaponized Supply Chains
China’s stranglehold on RREs and their dominant role in the manufacturing of critical input components that rely on them increasingly puts the US in an untenable situation. Recent escalations in trade tensions between the world's two largest super powers highlights this.
- December 2024 - China imposed export bans on gallium, germanium, antimony, and graphite, citing their strategic military and industrial importance.
- February 2025 - China further restricted exports of lithium processing technology, halting the supply of key materials like sorbent, impacting US battery production.
These actions are in direct response to U.S. imposed export controls, including ones aimed at limiting China's access to advanced microchips and semiconductor manufacturing equipment - like NVIDIA H100 GPU chips.
Government Support of Rare Earth Refining
Recognizing the strategic vulnerability of this dependence, the U.S. and its allies have begun implementing measures to rebuild domestic refining capacity and diversify supply chains. However, progress will be slow, and meaningful detangling from China’s REE dominance could take years, leaving critical industries exposed to geopolitical risks in the meantime.
Since 2020, the U.S. Department of Defense (DoD) has invested over $439 million to solidify domestic rare earth supply chains, particularly focused on bringing more refining capacity online.
- MP Materials operates the Mountain Pass Mine in California, the United States' only active rare earth mining and processing facility. The company has been awarded $45 million in contracts from the U.S. Department of Defense to support the development of a resilient rare earth supply chain. MP Materials specializes in the production of Neodymium-Praseodymium (NdPr), a vital component in high-strength permanent magnets used in electric vehicles, missile guidance systems, satellites, and computing hardware. In 2024, the company produced approximately 1,300 metric tons of NdPr oxide at Mountain Pass, accounting for roughly 3% of global supply, reinforcing its role in the U.S. effort to reduce reliance on foreign sources.
- In August 2023, Lynas Rare Earths was awarded a $258 million contract to construct a heavy rare earth (HRE) separation facility in Texas. As the world’s largest producer of separated rare earth elements outside of China, Lynas operates the Mt Weld mine in Western Australia, home to one of the world’s richest rare earth deposits. The new Texas facility is expected to process 2,500 to 3,000 metric tons of heavy rare earths annually, including approximately 1,250 metric tons of NdPr. Once operational, the facility will play a pivotal role in meeting the U.S. Department of Defense’s strategic rare earth requirements, reducing reliance on foreign refining and bolstering supply chain security.
- The Halleck Creek Project in Wyoming, launched in 2022, represents a strategic initiative to develop one of the largest rare earth deposits in the United States. The project has a full-scale production capacity of 2,000 to 3,000 metric tons of NdPr oxide annually. While it has not received direct funding from the U.S. Department of Defense, the project secured up to $456 million in debt financing from the Export-Import Bank of the United States in September 2024.
- The Saskatchewan Research Council (SRC) Rare Earth Processing Facility became operational in mid-2024, bolstered by over $100 million in funding from the Canadian government. As Canada’s first fully integrated rare earth processing facility, it is expected to produce 400 metric tons of NdPr metal per year, sourced from domestically extracted ore.
The public sector, led by the U.S. Department of Defense and Department of Energy has implemented other measures to bolster our domestic capabilities, including established strategic partnerships to develop resilient REE supply chains among allied nations, notably Australia and Canada. In addition:
- The National Defense Authorization Acts (NDAAs) recently expanded restrictions, prohibiting the acquisition of certain sensitive materials—including rare earth permanent magnets refined, separated, melted, or manufactured in China. These restrictions are set to take effect by January 2027.
- Starting no earlier than June 2025, contractors providing systems containing permanent magnets with rare earths or strategic materials must disclose the origin of these magnets and must establish supply chain tracking systems to ensure transparency.
Technology Must Lead the Way
The public sector will play a key role in reducing our dependence on China but there are limitations. The DoD can mandate where REEs and components originate from as part of government contracts, but controlling where the private sector procures these inputs is much more nuanced. Subsidies and tariffs are one option, and will give an emerging class of supply chain participants the opportunity to emerge, but it's not the long term answer. China’s lower labor costs, and government subsidies, will always make U.S. operations less economically competitive as currently constructed.
To win, it is crucial for the U.S. to establish new rare earth refining capacity, however, equally important is exploring innovative approaches to securing rare earth elements.
1. Refining from mining waste
Massive volumes of mining waste contain untapped REE reserves. Instead of traditional mining, companies can use innovative chemical, biochemical, or physical processes to recover REEs from mining waste streams. The U.S. Department of Energy has identified billions of tons of coal waste, ash, mine tailings, and acid mine drainage across the country which could significantly boost domestic supply of REEs. Research led by the University of Texas at Austin indicates that coal ash from power plants across the U.S. could contain up to 11 million tons of REEs, valued at approximately $8.4 billion
Phoenix Tailings is a Massachusetts-based company specializing in the sustainable extraction of rare earth elements from coal mining waste, commonly known as tailings. Their innovative process utilizes water and recyclable solvents to collect oxidized metals from these tailings, followed by electrochemical methods to isolate pure rare earth metals. They aim to produce over 3,000 tons of rare earth metals by 2026, potentially accounting for about 7% of the U.S. production at that time.
2. Recycling from end-of-life products
A new wave of startups is emerging to address the challenge of recovering critical raw materials from end-of-life technologies, including electric vehicle motors and data center electronic waste. With less than 1% of rare earth magnets currently being recycled, these companies are pioneering innovative solutions to establish a sustainable, circular supply chain for critical minerals.
- Redwood Materials, founded by former Tesla CTO J.B. Straubel, has raised approximately $1.8 billion to develop a closed-loop system for electric vehicle batteries. The company focuses on extracting rare earth elements from lithium-ion batteries, reducing dependence on newly mined materials.
- Cyclic Materials employs an advanced hydrometallurgical process to recover high-value rare earth elements such as neodymium and praseodymium from e-waste and end-of-life products.
- Noveon Magnetics specializes in the recycling of NdFeB (neodymium-iron-boron) magnets from discarded hard disk drives and other electronic waste.
3. Deposit discovery
AI and ML are being leveraged in mineral exploration to analyze vast geological datasets to predict the location of rare earth element deposits. By training on decades of geochemical surveys, satellite imagery, geophysical maps, and drilling records, ML models can identify subtle patterns indicative of mineralization—patterns that might otherwise go undetected by human geologists. Traditionally, deposit discovery has been an expensive, time-consuming process with less than 1% of exploration targets leading to viable mines. AI dramatically accelerates this process, identifying high-probability drill targets and significantly improving the efficiency of exploration efforts. Leading companies in this space, such as KoBold Metals and Earth AI, are at the forefront of leveraging AI for next-generation resource discovery.
Beyond exploration, AI is also transforming drilling and core sample analysis, optimizing drill site selection and enabling real-time classification of rock samples, reducing errors and minimizing wasted resources. Additionally, autonomous exploration technologies, including AI-powered drones and robotic vehicles, are enhancing access to hazardous or remote locations, making mineral assessments safer, faster, and more comprehensive.
4. Developing alternative materials to replace traditional REEs
Rare-earth-free alternative materials are emerging to replace traditional rare earth elements in critical technologies. The core idea is to develop new magnets, alloys, and components using abundant elements (like iron, nitrogen, aluminum, etc.) or novel designs so that devices such as electric motors, AI hardware, sensors, and high-strength composites no longer rely on critical rare earth elements.
One pioneering company in this space is Niron Magnetics, which is developing high-performance, rare-earth-free permanent magnets using an iron-nitrogen compound instead of conventional neodymium or praseodymium-based magnets.
Conclusion
Securing a stable and diversified supply of rare earth elements is critical to the United States’ economic resilience and national security. While government investments in domestic mining and refining are essential, the long-term solution lies in technological innovation, including REE recycling, mining waste recovery, AI-driven exploration, and the development of alternative materials. By embracing these advancements, the U.S. can reduce dependence on foreign supply chains, strengthen its manufacturing capabilities, and position itself as a leader in the next generation of critical materials innovation.
James Murphy is Forum’s Managing Partner, leading the Investment team in finding bold, ambitious SaaS founders. Connect with him on Linkedin and X.
Latest Thought Pieces
.avif)